1.はじめに
今回は、レーザ焼入れと高周波焼入れの7つの違いについて解説を行います。高周波焼入れとレーザ焼入れは同じ部分焼入れという表面処理加工の非常に近しい技術になります。しかし、加熱プロセスや冷却プロセス、焼入れ品質管理項目など様々な違いがあります。それぞれの技術に対しての違いを知ることで、両技術の効果的な使い分けが出来ると考えます。今回は、その違いを「7つ」に分類して解説を行います。
2.レーザ焼入れと高周波焼入れ7つの違い
2-1 加熱方法
熱処理において最も重要なプロセスは、加熱プロセスです。高周波焼入れとレーザ焼入れとでは、全く別の方式で金属に対して加熱を行います。高周波加熱は誘導加熱による加熱プロセスになります。その際、コイルに高周波電流を流し磁界を発生させ、その中に加熱する金属を置くと、その金属内にコイルに流した電流の向きと逆向きの渦電流が発生し、被加熱物金属表面に電流が流れ、誘導加熱が発生します。従って、高周波加熱のプロセスでは、加熱コイルが必要になります。また、そのコイルの位置や形状を制御することで、選択的に部分加熱することができます。(Fig.1)
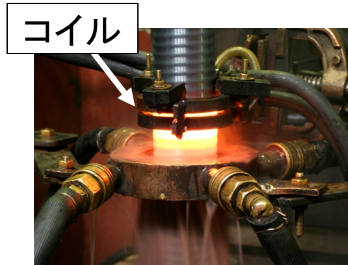
次にレーザ焼入れでは、レーザ発振器から照射されたレーザ光がファイバー、光学系を介して、ワークに照射された部分のみ加熱されます。(Fig.2)。レーザ焼入れの場合は、様々なビーム形状を作るためには、コイルではなく、様々な種類の光学系が必要になります。

2-2 冷却方法
熱処理プロセスにおいての冷却も、非常に重要な要素となります。一般的に熱処理での冷却方法の種類として、炉冷、空冷、ガス冷、油冷、水冷のように様々な種類があります。
高周波焼入れでは、主に水冷と油冷が使われています(Fig.3)。水冷の場合は、コイルで加熱した直後に水冷ジャケットで冷却水を噴射し、冷却を行います。冷却に関しても、水量、水圧、水温などの管理が重要になります。また、水冷をするための循環タンクやポンプ、配管等のイニシャルコストや冷却剤などのランニングコストが必要となります。また、油冷の場合では、油の購入のみならず、廃棄するときにもコストがかかり、廃液処理を業者に依頼することが一般的です。
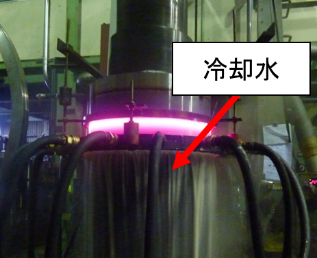
一方、自己冷却が一般的なレーザ焼入れの場合は、冷却に関する設備は一切必要無く、高度な管理等も必要ないため、冷却における管理やコストが必要なくなります(Fig.4)。高周波焼入れでは、加熱プロセスと冷却プロセスの管理をしなければなりませんが、レーザ焼入れでは、加熱プロセスの管理のみで良いということになります。そのため、管理工数が単純に半分となり、工程能力(Cpk)も高い数値が出やすくなります。
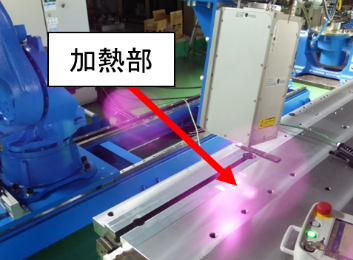
レーザ焼入れの自己冷却について、以下の実験を行い、急冷できているのかを測定を行いました。50mm×50mm×10tのS45C材に10mm幅のレーザ焼入れを実施しました。その際、表面部の温度分布をサーモグラフィーで、温度測定した際の任意の点における温度分布をFig.5で示します。レーザが通過する時にワーク温度は、常温から約0.8秒で約970℃程度まで昇温しており、その時の昇温速度は、1,200℃/secとなります。そして、レーザ光が通過した後に、自己冷却により、ワーク内部での熱伝導により、S45CのMs点(約500℃)まで、1200℃/secの速度で冷却されています。熱処理で割れが出やすいMf点(約250℃)付近の冷却が、強制冷却ではなく、自己冷却のため、比較的ゆっくりと冷却されます。水冷を行い常温付近まで一気に冷却された場合、割れが発生する危険性が高くなりますが、自己冷却の場合では、ワーク内部の残熱により、割れ危険域(Mf点付近)でゆっくり冷却されるため、割れが出にくいというメカニズムになっています。
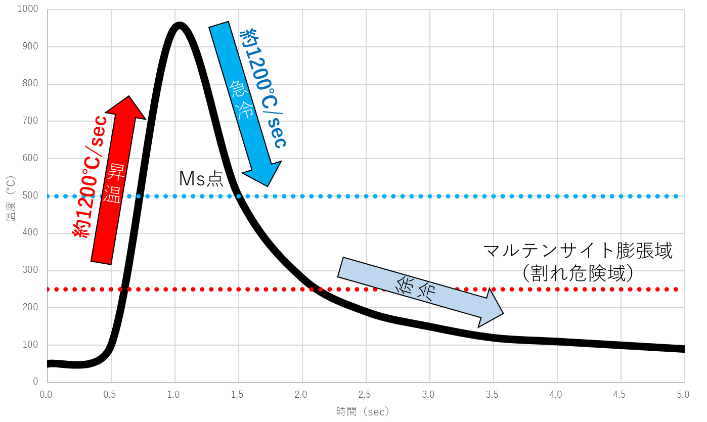
早い昇温速度と冷却速度を満たし、そして割れ危険域はゆっくり冷却されるという熱処理の冷却プロセスにおいては、理想的な冷却カーブが自己冷却で達成できています。これらの効果により、レーザ焼入れで出来る金属組織は、微細なマルテンサイト&割れにくい組織が出来やすいと言えます。しかし、この現象は今回のワークでの現象ということをご承知ください。
関連動画
2-3 焼入れ範囲
高周波焼入れとレーザ焼入れは同じ金属の部分焼入れですが、焼入れ範囲にも違いがあります。高周波焼入れの場合は、コイルさえ製作出来れば、様々な形状に対して部分焼入れが可能です(Fig.6)。従って、コイルでカバーが可能な広い範囲を一気に加熱することができます。また、複雑形状でも対応は可能な場合があります。しかし、コイルを製作しなければならないという制約下では、10mm以下の範囲を加熱する場合には、コイル製作は困難になります。
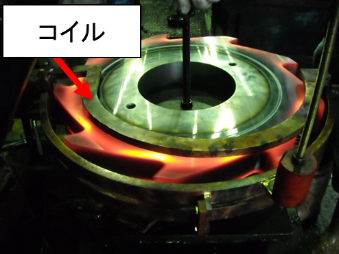
レーザ焼入れの場合において、レーザ光の幅に制約が出てきます。富士高周波においては、現在、約100mm幅までは対応できますが、100mm以上の幅となると一度に加熱することは不可能になります。しかし、0.5mm程度の狭い範囲の部分焼入れは可能になります。つまり、レーザ焼入れは、より精密な部分焼入れができ、ピンポイントで加熱できるため、焼入れ範囲以外に対して熱影響が少ないといった利点が挙げられます。
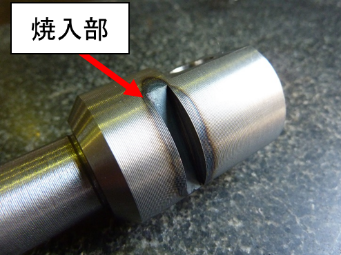
先ほど、弊社では最大100mm幅までの焼入れ幅とお伝えしましたが、より広い範囲をレーザ焼入れで硬くしてほしいという依頼をいただきます。それらのワークは、プレート物やレール物のような薄肉、長尺系のワーク(Fig.8)になります。
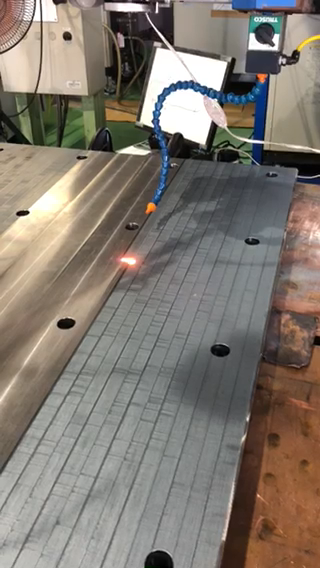
その場合、ある問題を除けば、お客様のニーズにお応えすることができます。その問題というのが、「ソフトゾーン」の問題です。広範囲の表面に対して、複数回レーザ光を照射した場合、重なり合うところがソフトゾーンになります。実際、ソフトゾーンがどのような硬度分布になるのかの実験を行いました。Fig.9に示されているように、40mm×100mm×10tのワークに22mm幅でレーザ焼入れを行いました。
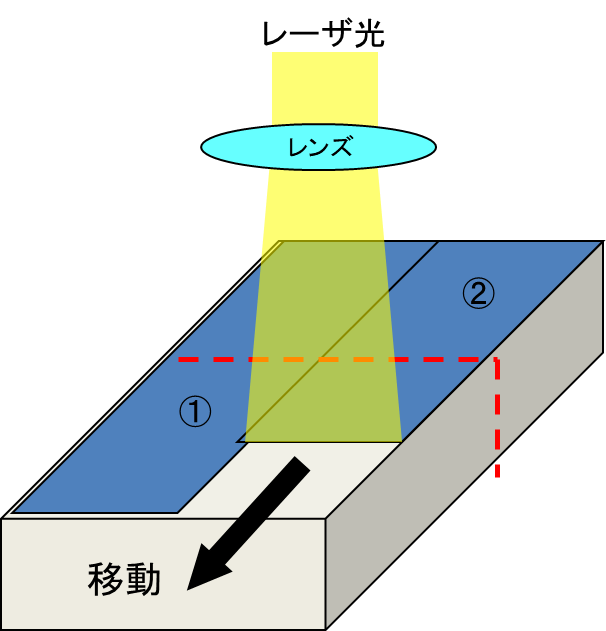
レーザ出力:2000W
レーザ走査速度:50cm/min
スポット径:22mm×10mm
焼入方法:約1.5mmオーバーラップにてレーザ焼入れ
検査方法:赤点線部を切断研磨後、MV測定器にて表面から0.3mmの位置を0.1mmピッチにて測定
2ライン目は、1本目のラインに対して、約1.5mmラップさせています。焼入れ後、中央部を走査方向に対して垂直方向で切断し、切断面に対して、表面から0.3mmの位置をマイクロビッカース硬度計で、0.1mmピッチで1ライン目から測定を行いました。その硬度結果と組織写真をFig.10に示します。薄い茶色の部分がマルテンサイト組織となっており、濃い茶色の部分が1本目のマルテンサイト組織が、2本目のレーザ焼入れによって、焼戻しされた範囲(焼戻しマルテンサイト)となっています。硬度結果に示されている通り、焼戻しマルテンサイトの部分は、HV400程度まで硬度が下がっている箇所があります。その部分がソフトゾーンになります。広い範囲を硬化させるために、何ラインもレーザ焼入れをする場合、焼入れが重なるごとソフトゾーンが発生し、その距離は、約2mm、硬度はHV400程度まで低下します。しかし、これは、あくまで一例で、材質や硬化層深さなどが変わるとソフトゾーンの距離や硬さは変わります。
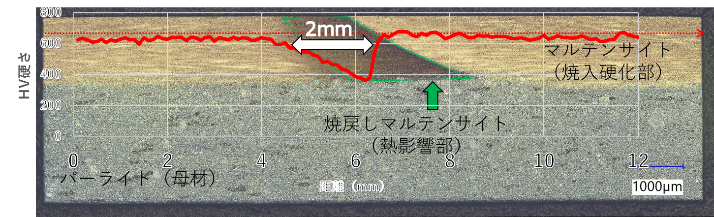
関連動画
2-4 硬化層深さ
金属の熱処理において、重要な品質管理項目として、有効硬化層深さがあります。これも高周波焼入れとレーザ焼入れでは違いがあります。弊社において、1mmを一つの境界線としており、1mm以上の硬化層深さが必要な場合は、高周波焼入れを推奨しており、逆に1mm以下の硬化層深さが必要な場合は、レーザ焼入れを推奨しています。Fig.11でギヤの焼入れパターンを示しています。高周波焼入れは、有効硬化層深さ1~5mm程度が得意となり、レーザ焼入れの場合、有効硬化層深さ0.3~0.8mmが得意の硬化層範囲となります。実際は、高周波焼入れでも硬化層深さが浅いのが出来ないのかというと、コイルと周波数の高い発振器があれば、対応は可能で、レーザ焼入れにおいても決して1mm以上の硬化層深さが出来ないわけではありません。しかし、レーザ焼入れ特有の自己冷却では、冷却速度が足らなくなるため、水冷や油冷などの強制冷却が必要となってきます。
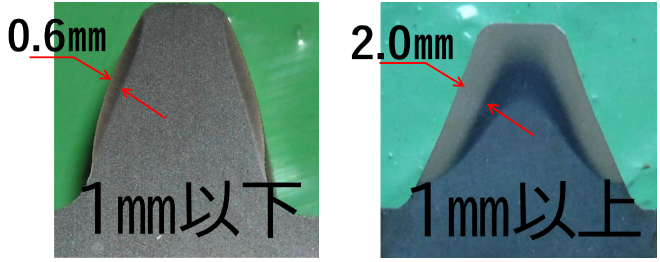
2-5 焼入れ硬度
焼入れ硬度は、硬化層深さと同様に金属の熱処理においては、重要な品質管理項目になります。Table1に代表的な材質の高周波焼入れ硬度とレーザ焼入れ硬度を示しています。Table1からわかるように高周波焼入れとレーザ焼入れでは、硬度に大きな違いはありません。少しだけ、レーザの方が高硬度になりやすい程度で、硬さに関しては、材質に含まれているカーボン量で決定されます。
【Table1 各材質における高周波とレーザの焼入硬度】
S45C | SCM440 | SK5 | FCD600 | SUS420J2 | SKD11 | |
高周波 | HRC 52〜60 |
HRC 52〜57 |
HRC 55〜63 |
HRC 45〜52 |
HRC 45〜55 |
HRC 55〜60 |
レーザ | HRC 55〜60 |
HRC 55〜60 |
HRC 60〜65 |
HRC 52〜60 |
HRC 45〜50 |
適さない |
高周波焼入れやレーザ焼入れで良く利用されているS45CやSCM440は、調質(焼入れ焼戻し)の有無により、熱処理品質は変わってきます。特にレーザ焼入れの場合は、超短時間加熱になるため、前熱処理の影響を受けやすくなります。今回は、SCM440 の調質材と非調質材でのレーザ焼入れの焼入れ性の違いについて調査を行いました。ワークサイズは、50mm×50mm×10t、スポットサイズは、15mm×5mm、移動速度は、80cm/min、出力は、2,000Wにて同条件で、レーザ焼入れを行いました(Fig.12)。
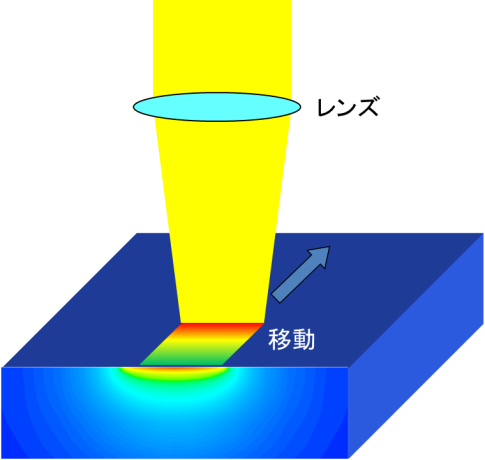
スポット径:15mm×5mm
移動速度:80cm/min
出力:2000W
材質①:SCM440(調質材)
材質②:SCM440(非調質材)
中央部を切断し、Fig.13のように表面からマイクロビッカース硬度計にて内部硬度の測定を行いました。
検査結果をFig.14に示します。表面硬度に関しては、調質材、非調質材ともにHV700程度となり、差はあまり見受けられません。しかし、0.4mmあたりからの内部硬さに差がではじめ、調質材は、0.8mmまでHV700を示しているのに対し、非調質材は、0.4mmあたりから徐々に硬度が低下しているのがわかります。これは、調質材の方が、焼入れ性が良いという結果になります。切断検査ができない、製品の硬化層深さを保証するには、調質材にした方が望ましいということがわかります。
【マイクロビッカース高度計にて、表面から0.1mmピッチにて測定】
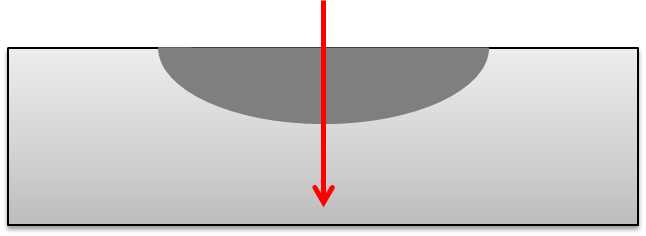

2-6 熱処理歪
レーザ焼入れは、一般的に高周波焼入れに比べ、歪の少ない熱処理方法として知られています。しかし、あくまで歪が少ないという事であり、歪が出ないという事ではありません。熱を加えて、硬化させるため、必ずどこかにマルテンサイト変態応力は発生し、歪はでます。ただ、その歪の大きさが、高周波と比較して小さい場合が多いということになります。Fig.15のようなワークに対して、高周波焼入れとレーザ焼入れでの歪量を比較しました。焼入れ箇所に関しては、Fig.16のように外周テーパー部になります。ワーク内径の変寸に関して、焼入れ前後で調査を行い、その結果をTable2に示します。
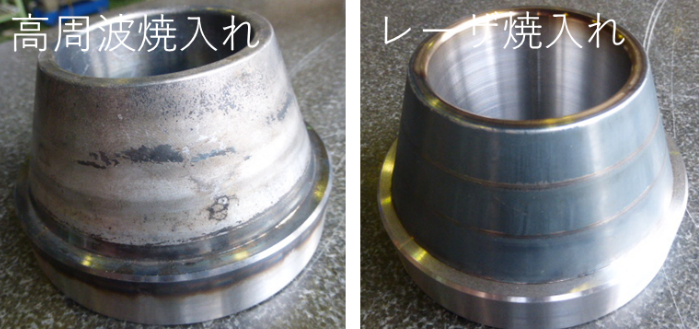
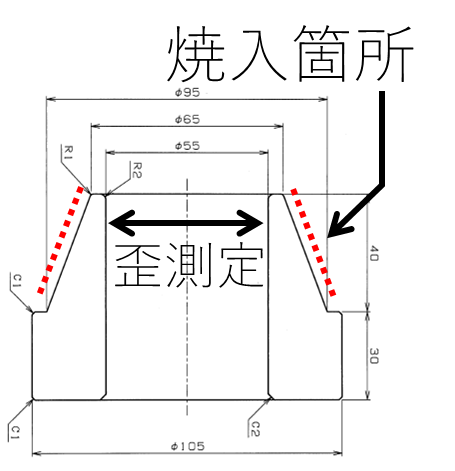
【Table2 歪量結果】
高周波 | レーザ | |
変形量 | +100μm | -5μm |
硬化層深さ | 1.5mm | 0.5mm |
関連動画
高周波焼入れでは、内径部が100μm大きくなり、レーザ焼入れでは、5μm小さくなっています。この結果から、レーザ焼入れの方が、歪がかなり小さくなっています。今度は、硬化層深さを見ると、高周波焼入れでは、1.5mm、レーザ焼入れで0.5mmと硬化層深さがレーザ焼入れの方が浅くなっています。従って、今回の実験結果から推測すれば、単純に硬化層深さが浅くなっているレーザ焼入れの方が、歪が小さいと考えられます。おそらく、高周波焼入れでも専用コイルを製作し、さらに、周波数の高い発振器で処理して、硬化層深さを0.5mm程度にすれば、同じような歪量になる可能性が高いと推測されます。2-4項にあるように高周波焼入れは1mm以上の硬化層深さが得意、レーザ焼入れは1mm以下の硬化層深さが得意なため、結果として硬化層が浅いレーザ焼入れのほうが、歪が小さくなっています。しかし、これまでの弊社の実績ベースでは、歪量の目安として、レーザ焼入れは高周波焼入れの1/10程度に抑えられると考えられます。
2-7 品質管理
最後に品質管理の違いについて解説を行います。Table3に熱処理の品質管理項目について示します。品質管理項目については、本来は、もっとたくさんの項目がありますが、代表的な項目だけを抜粋しています。
【Tabele3 品質管理項目】
ワーク管理 | 段取り | 加熱管理 | 冷却管理 | |
高周波 | 油分 | コイル形状 コイル位置 |
出力 加熱時間 速度 |
水量 水圧 水温 濃度 |
レーザ | 油分 錆 面粗度 色合い |
ビーム形状 照射位置 |
出力 加熱時間 速度 |
無し |
まず、ワーク管理についてですが、高周波焼入れの場合、油分の付着状況を管理する必要性はありますが、そこまで繊細になる必要はありません。しかし、レーザ焼入れの場合、ワークに油分が付いていると、Fig.17のようにレーザでワークを加熱した時に油煙が発生します。その油煙がレーザ光を雲のように遮る形となり、レーザ光が油煙で減衰されてしまいます。従って、レーザ焼入れ前のワークに油分が付いていない事が重要になってきます。ただし、油煙をエアーで飛ばすと、油煙がレーザ光を遮らないので、焼入れ性に問題はでません。また、ワークのサビや面粗度、色合いも吸収率が変化してしまうため、十分に管理しなければならない項目になります。そのため、レーザ焼入れでは、焼入れ前ワークの状態管理を高周波と比較して十分に行う必要があります。
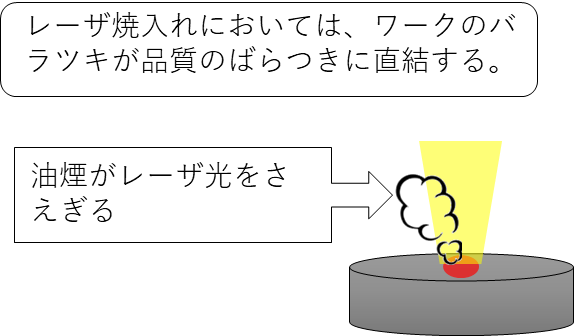
次に段取りに関する管理ですが、高周波焼入れの場合は、コイルの形状や位置などが管理項目の代表例になり、レーザ焼入れの場合は、ビームの形状や照射位置が管理項目の代表例になります。レーザの照射位置管理は、Fig.18のようにバーンペーパーを使ってワークのどの部分にレーザが当たっているのかを管理します。段取り管理は、設備の環境などによっても大きく違ってきます。従って、段取りに関わる高周波焼入れとレーザ焼入れの違いは大きく変わらないと言えます。
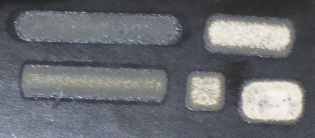
次に加熱管理ですが、出力、加熱時間、移動速度など、ほぼ高周波とレーザは同じ管理項目になります。レーザの出力は、Fig.19のパワーメーターを使って、照射位置での出力の管理ができます。加工点における実測値を管理することで、より精度の高い管理が可能となります。
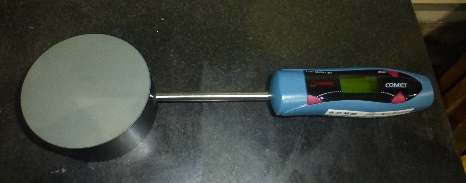
最後に冷却の管理ですが、高周波焼入れの場合、水量、水圧、水温、濃度など、管理すべき項目はたくさん出てきますが、自己冷却で冷却が出来るレーザ焼入れの場合、冷却に関する管理項目はありません。その点では、レーザ焼入れは非常に品質が安定しやすいと言えます。
3.まとめ
レーザ焼入れと高周波焼入れの違いについて、7つに分類して解説を行いました。細かく見れば、もっとたくさんの違いはありますが、このように同じ部分焼入れ技術である高周波焼入れとレーザ焼入れでも、ここまで様々な違いが有るという事に気づかれたかと思います。設備的な管理は違えども、ワークに対する品質管理は、有効硬化層深さ、表面硬さ、焼入れ範囲等全く同じになります。という事は、高周波焼入れにおける品質管理を熟知していれば、レーザ焼入れの品質管理も問題無くできます。
関連サービス
この記事の執筆者
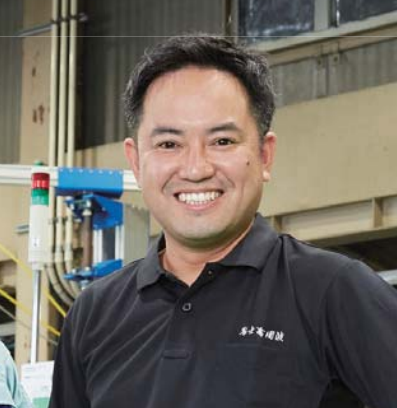
富士高周波工業株式会社 代表取締役
後藤 光宏
特級金属熱処理技能士/レーザ加工管理技術者名誉1級/滋賀県立大学 博士課程 在学中
小学生から大学までは野球漬けの日々を送る。
大学卒業後はポンプメーカーに1年間従事した後、2004年に富士高周波工業(株)に入社。
2008年からレーザ焼入れの開発に従事し、2018年に代表取締役に就任。
オンライン名刺はこちら