1.はじめに
今回は、レーザ焼入れの基礎的な技術や、レーザ焼入れの技術的特徴、レーザ焼入れによって出来る金属組織、温度分布などについての解説になります。
2.金属の部分焼入れ
金属の部分焼入れとは、読んで字のごとく金属を部分的に加熱し、冷却することによって部分的に硬化させる技術の事です。近い技術としては、高周波焼入れやフレームハードが挙げられます。
また、部分的に硬くするのではなく、表面全体を硬化する手法としては、浸炭焼入れや窒化処理があります。それぞれの違いのイメージをFig.1に記載しております。一般的に表面全体を硬くする浸炭焼入れや窒化処理は、炉の中に製品を投入し、焼入れ処理を行いますが、高周波焼入れやレーザ焼入れのように部分的に硬化させる処理は、炉の中で処理は行いません。
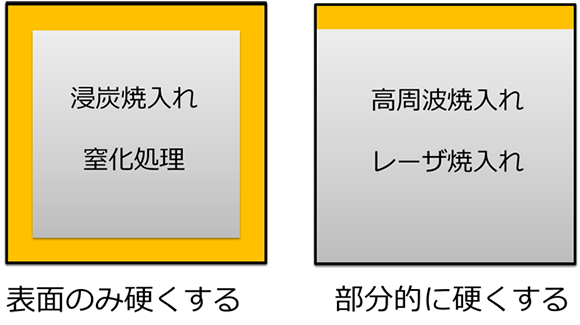
部分的に硬くするメリットとしては、焼入れ後の加工の際、軟らかい部分に関しては、切削加工がしやすいというメリットがあります。ただし、炉による処理と違い、一度に数多くの製品を同時に処理することができないので、基本的には1ヶずつの処理となります。
3.様々なレーザ加工法
レーザ加工には様々な加工方法が存在し、加工用、医療用、計測用、軍需用など、あまりにも多岐にわたるため、ここでは一般的にレーザ熱加工と言われる産業用の用途のみに絞って解説を行います。
まずは、レーザを使った切断加工で、これはレーザ光を小さく絞り(φ0.1程度)、金属の板を高速で切断を行います。レーザの産業用途としては、最もポピュラーな加工方法となります。この切断技術を応用して、高速穴あけ技術などがあります。
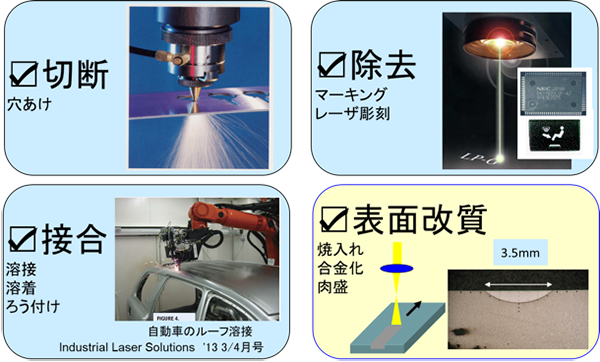
次の加工方法は、接合でレーザ溶接とも言われます。ファイバーレーザの登場により、一気に市場が広がってきました。これはレーザを用いて、金属の接着面を溶融させ、金属同士つなぎ合わせます。薄板の低歪溶接などに使われることが多い技術となります。その他の応用分野として、銀ロウなどを用いたレーザロウ付けなどがあります。
次に、レーザによる除去加工が挙げられます。除去加工と聞くとイメージが湧きにくいかと思いますが、代表とされる技術は、レーザマーキングになります。これは、出力の小さいレーザ発振器でも施工可能な技術になるため、製造業のみならずあらゆる業界で利用されているレーザ加工方法です。
そして、最後にレーザ表面改質についての解説になります。レーザ焼入れやクラッディングは、この表面改質技術に分類されます。レーザ光を使用して、表面を加熱したり、肉盛り(クラッディング)をしたりする技術になります。このようにレーザ加工には様々な加工方法が存在しますが、弊社では、レーザを使用した表面改質技術を得意としています。
関連動画
4.レーザ焼入れの原理
レーザ焼入れの基本的な原理についての解説になります。Fig.3の模式図のレンズと記載されている部分にレーザ光が透過することにより、レーザは任意の形状に集光されます。集光される形状としては、半導体レーザを用いたレーザ焼入れの場合、矩形に集光して利用することが一般的になります。まず、第一段階として、任意のビーム形状でワークを照射し、ワーク温度が約1,000℃に達したら、レーザ光を移動させます。その結果、レーザ光によって加熱された部分は、熱伝導により熱はワーク内部に拡散します。そのため、レーザ光が通過した瞬間から熱伝導による冷却が始まります。
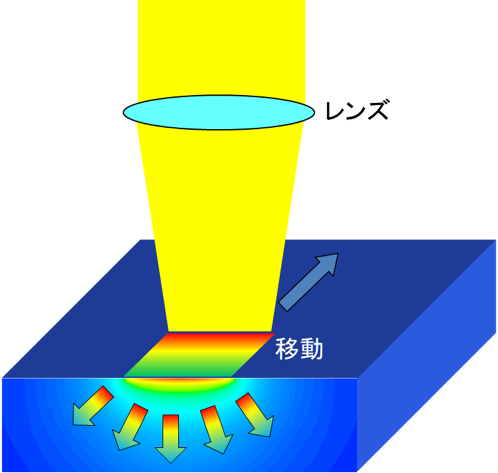
焼入れでは、ある一定の冷却速度で冷却をしなければ、硬化しません。しかし、レーザ焼入れの場合、ピンポイントでの加熱になるため、硬化させるための十分な冷却速度を確保することができます。そのため、レーザによって加熱された部分は焼入れ硬化します。この熱伝導のみで冷却され、硬化する現象を自己冷却と呼び、一般的にレーザ焼入れは、水や油を使用しない自己冷却によって焼入れ硬化する技術になります。
5.レーザ焼入れの温度分布と金属組織
レーザ焼入れの温度分布と金属組織について解説します。レーザ焼入れは表面からのレーザ光による加熱で焼入れ硬化させる技術です。よって、Fig.4のように表面部の温度は高く内部に向かうにつれて、温度は低くなります。そのため、Fig.5のような硬化パターンになります。表面から、オーステナイト温度まで達した領域のみ焼入れ硬化し、オーステナイト温度領域以下の部分に関しては、母材硬度のままになります。Fig.5を見れば、わかるようにレーザ焼入れの場合は、一般的にビームの中心付近が端と比較して硬化層深さが深くなりやすく、端に向かうにしたがって硬化層深さが浅くなります。
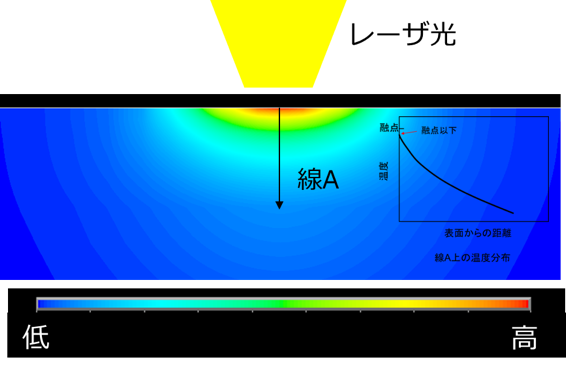
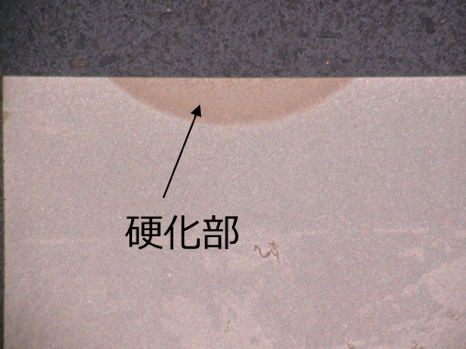
焼入れ硬化部を表面からミクロで観察した金属組織写真がFig.6になります。表面から0.5mmまでは一様なマルテンサイト組織を有していますが、0.5mmから0.9mmまでは、中間層と言われるマルテンサイト+フェライトの金属組織となっています。さらに内部に進むと、フェライト+パーライトの母材組織が観察できます。Fig.7は、表面からのビッカース硬さをプロットしたもので、一様なマルテンサイト部は、HV680程度を示していますが、中間層に関しては、内部にいくにしたがって、硬度低下がみられます。そして、母材の部分に入るとHV220程度で硬度は安定します。
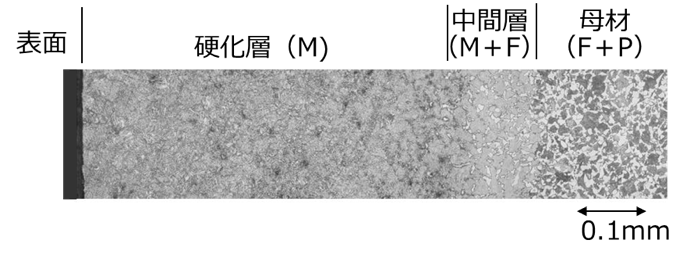
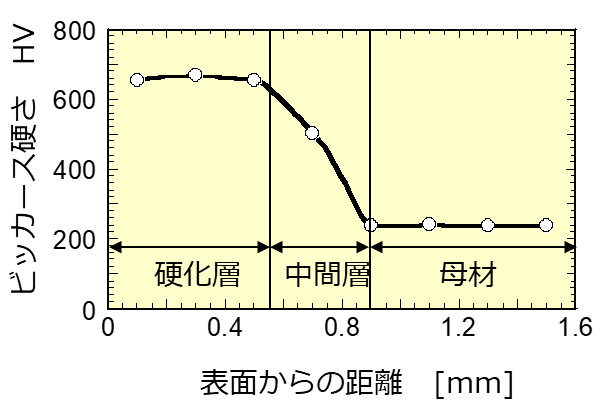
6.なぜレーザ焼入れが注目されるのか
レーザ焼入れの特徴として、他の熱処理と比較して次の2点がメリットとして挙げられます。冷却時に水、油を使わない(Fig.8)。消費電力が少ない。といった点がメリットとして挙げられます。歪が少ないというメリットもありますが、これは形状や熱処理方法によって歪低減の効果が変化するので、今回は、割愛させていただきます。
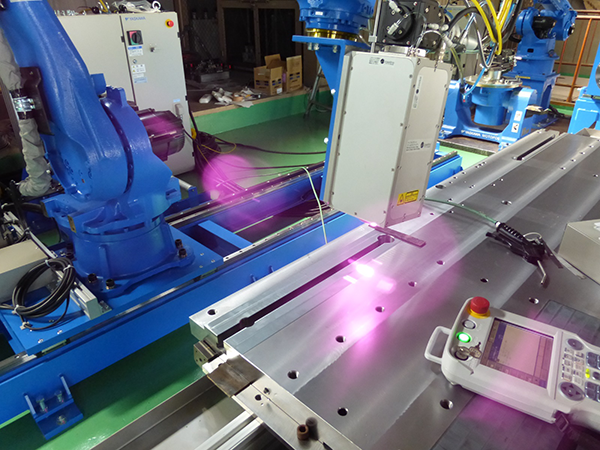
まずは、冷却についてですが、水や油を使わない事で、冷却剤や油の購入のコストを削減することができます。弊社の高周波事業部においては、年間数百万円分の冷却剤や油の購入が必要となりますが、レーザ事業部においては、それらの購入費用がほぼありません。また、冷却工程を無くすということは、冷却用のポンプやタンクなど設備が不必要になり、イニシャルコストとランニングコストの削減に大きなメリットがあります。
次に、消費電力が少ないというメリットがあります。レーザ焼入れに使用されるレーザ発振器は、主に1~5KW程度の出力のレーザ発振器になります。2021年現在のレーザ発振器の電気-光変換効率は、60%程度あり、5KWのレーザ発振器を稼働するにあたり、チラーなどの周りの設備も含めて20~30KWの電力で稼働が可能です。逆に弊社の高周波発振器の場合、一般的に30~200KWの設備がメインで稼働しています。高周波発振器は、変換効率が90%程度ありますが、元々の電力は最低でも40KW程度必要になります。よって、レーザ発振器と比較して大きく電力量を使います。富士高周波は、高周波焼入れの工場とレーザ焼入れの工場は分かれており、それぞれの工場での電力は、両工場で、同じ売上げだったと仮定した場合、約4倍(2018年実績)の差があります。熱処理業において、電気代というのは経費の中でも大きなウエイトを占めており、そのため、熱処理における消費電力量の削減は大きいメリットと言えます。
7.まとめ
ここまで、レーザ焼入れの基礎的な事を解説してきました。レーザ焼入れはまだまだ認知度が低い技術になりますが、弊社が事業を開始した2008年12月からは、徐々に広がりを見せてきています。当時と比べ、レーザ発振器の価格も大きく低下していることも大きな要因と考えられます。この技術を活用するためには、まずは、このレーザ焼入れという技術がどのような技術なのか知って頂く事が重要と考えています。
関連サービス
この記事の執筆者
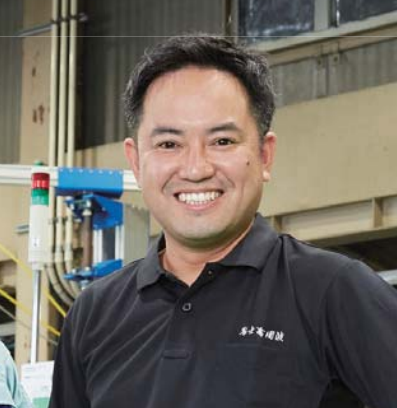
富士高周波工業株式会社 代表取締役
後藤 光宏
特級金属熱処理技能士/レーザ加工管理技術者名誉1級/滋賀県立大学 博士課程 在学中
小学生から大学までは野球漬けの日々を送る。
大学卒業後はポンプメーカーに1年間従事した後、2004年に富士高周波工業(株)に入社。
2008年からレーザ焼入れの開発に従事し、2018年に代表取締役に就任。
オンライン名刺はこちら