1.はじめに
今回は、従来の熱処理で困っていたことを、レーザ焼入れでどのようにして解決したのかをポイントを交えて解説します。
2.課題解決事例
2-1 課題解決事例①
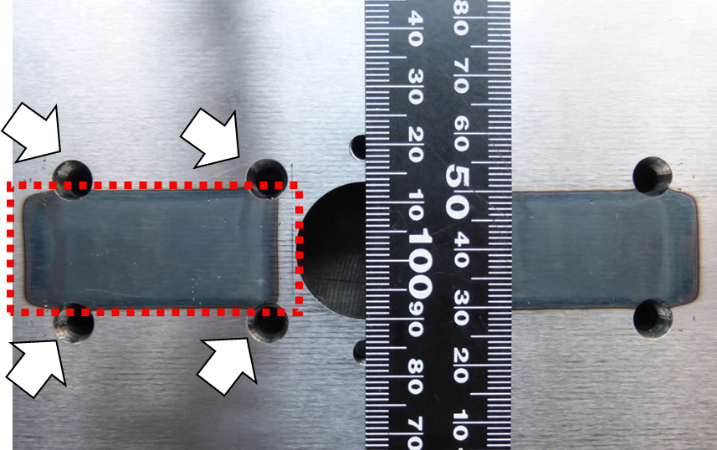
Fig.1のワークは、4つの小さい穴と中央に大きな穴がある金型部品になり、割れの危険を回避しながら、品質の安定化を達成した事例になります。このワークでは、赤枠で囲った部分に相手部品が当たるため、この部分のみを硬くしたいとのニーズがありました。本ワークのサイズは大きいですが、硬くしたい部分は、20mm×50mm程度の範囲だけになります。しかし、本ワークは、同じ部分焼入れでも高周波焼入れでの加工は、難しい案件になります。なぜなら、高周波焼入れの場合、20mm×50mmの範囲を硬化するために不必要な部分まで加熱してしまう可能性が高いからです。
その理由として、Fig.1矢印の4つの穴部分が、加熱時に高周波焼入れのエッジ効果で、オーバーヒートし溶融してしまう危険性や、水や油などでの冷却時に過冷却になりやすく、クラックが入ってしまう危険性が高くなるからです。
そこで、レーザ焼入れを適用すれば、高周波焼入れのようにエッジ効果がないため、穴部付近がオーバーヒートせず、また、レーザ焼入れ特有の自己冷却により、マルテンサイト膨張域でゆっくり冷却されるため、割れも発生しにくくなります。そのため、硬さが必要な部分のみを割れリスクゼロで部分的な硬化を実現した事例になります。
関連動画
2-2 課題解決事例②
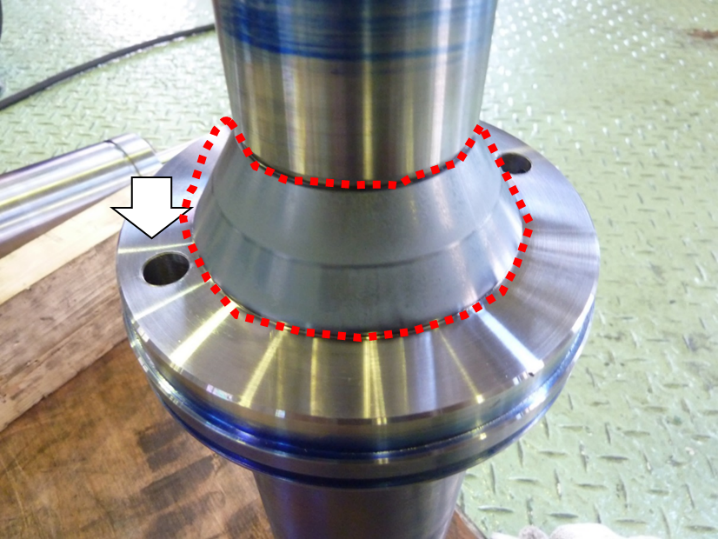
Fig.2のワークでは、高周波焼入れと比較し、単品物のコストダウンと工期短縮につながった事例になります。
本ワークは、シャフト部分とフランジ部分のテーパ形状でつながっており、赤枠のテーパ部のみを硬化したいという要求でした。さらに、Fig.2矢印のフランジ部分には熱影響を与えたくないと、とても厳しい熱処理要求がありました。高周波焼入れの場合、専用コイルを製作する必要があり、その製作費用も数万円ほどかかるため、熱処理費用が大きく上がってしまうという課題もあります。実際、本ワークは単品物で、受注個数は1ヶだけでした。その1ヶのために数万円かかるコイルを製作していては、お客様が求めるコストに、まったく合いませんでした。
そこで、レーザ焼入れを適用すれば、テーパ部のみ硬化させ、フランジなどにほとんど熱影響を与えず焼入れできました。また、専用コイルを作る必要性も無く、コイル製作費のコスト削減と、コイルを製作する時間も削減でき、工期の短縮につながりました。以上のように、狙った部分のみ焼入れできるというのは、様々なメリットがあります。
関連動画
2-3 課題解決事例③
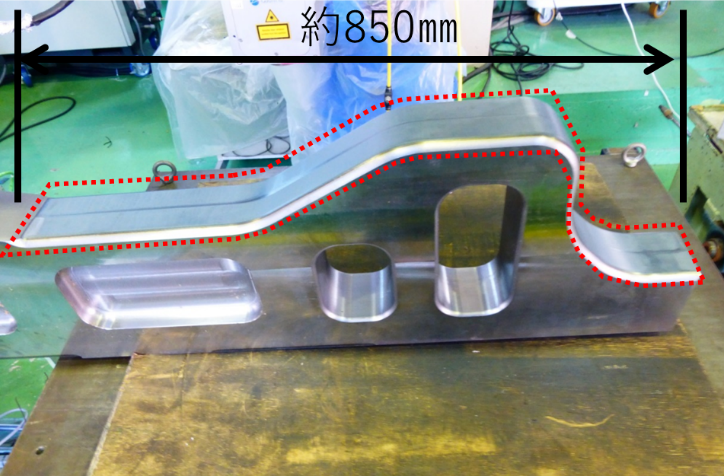
Fig.3のワークでは、複雑形状品の部分焼入れにおいて、時間をかけずに最短で焼入れを行った事例になります。Fig.3にあるように複雑な曲線を描いており、赤枠部のみを硬化したいとの要望でした。また、本案件のワークは、形状的に複雑かつ全長が約850mmもある重量物でした。
この複雑形状かつ重量物である、ワークの赤枠部を高周波焼入れするためには、高周波焼入れコイルを3次元で自在に動かすか、ワークを300kg可搬以上の6軸ロボットで、ハンドリングさせながら、自在に動かす必要性があります。しかし、弊社には、そのような設備がないため、高周波焼入れをすることはできない案件でした。
一方、レーザ焼入れシステムは、6軸ロボットの先端に光学系が取り付けられています。そのため、ティーチングさえすれば、レーザ光を自由自在に動かすことが可能となります。従って、このような複雑形状かつ重量物のワークを動かさずに、レーザ光を3次元的に動かしながら、焼入れする事が可能になります。また、このようなワークは、一般的には段取りが大変ですが、レーザ焼入れの場合、ワークを作業台に置き、ティーチングをするのみでレーザ焼入れが可能になります。実際に、段取りから焼入れ完了まで約1.5時間で作業を完了させることもできました。
このように、レーザ焼入れでは、レーザ光を6軸ロボットの先端に取り付けて光を自由自在に動かして焼入れする事が多いので、複雑形状のワークに対応ができるというメリットがあります。
2-4 課題解決事例④
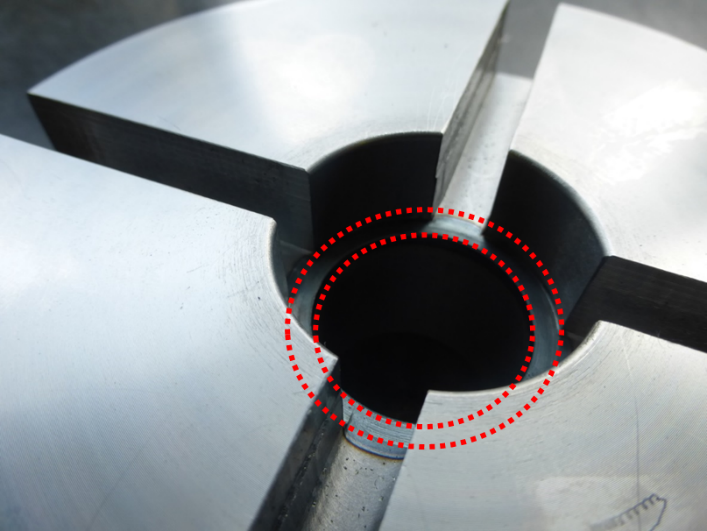
Fig.4のワークでは、奥まった箇所への部分焼入れの事例について紹介します。このワークは、円柱状の形状をしたワークで、中央部に段差のある穴があり、その中央部の穴の段差部分の端面だけを硬化したいという案件でした。もし、この段差部分のみを高周波で硬化させようとすると、Fig.5のように内径部ごと硬化させなくてはなりません。その焼入れ方法では、ふたつの懸念事項が出てきます。まず一つが、高周波焼入れによって、Fig.5の矢印のように内径寸法が縮むということです。高周波焼入れだと、内径部まで、硬化しマルテンサイト膨張によって、内径が小さくなってしまいます。内径部の公差が厳しい場合、後加工を必要とする可能性が高くなります。そのため、内径部を仕上げるといった、後工程が増えてしまい、コストアップにつながります。また、もう一つの懸念事項は、高周波焼入れのエッジ効果によって、段差エッジ部がオーバーヒートかつ過冷却によって、割れが発生しやすくなるといった懸念事項です。
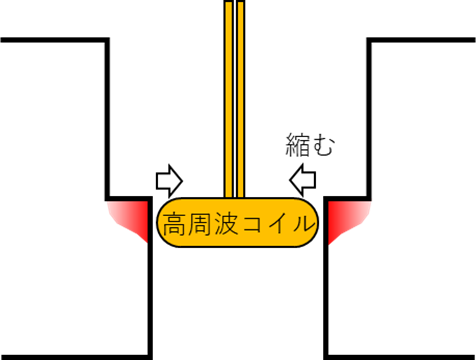
それらの懸念事項に対して、レーザ焼入れで以下のように解決しました。レーザ焼入れでは、奥まった部位であっても、光さえ届けば、Fig.6 のように硬化させたい内径段差部分のみを硬化させることが可能です。内径側面部をほとんど硬化させないため、内径部の縮みは回避することができます。つまり、内径部が縮まないということは、後加工もする必要性が無く、工程短縮、コストダウンにつながります。また、エッジ効果による割れ懸念も回避できます。以上のように、レーザ光は光さえ届けば、奥まった部位を硬化させることができるという特徴があり、その特徴を上手に活用することで、部品設計、製作工程設計の幅が大きく広がります。
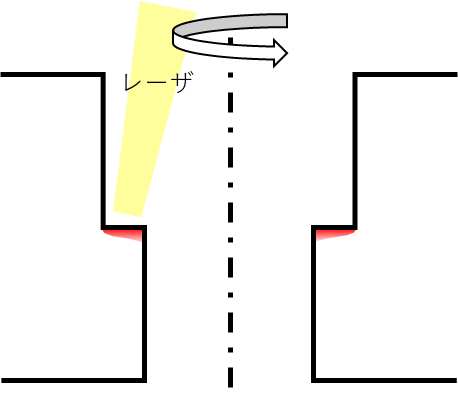
関連動画
2-5 課題解決事例⑤
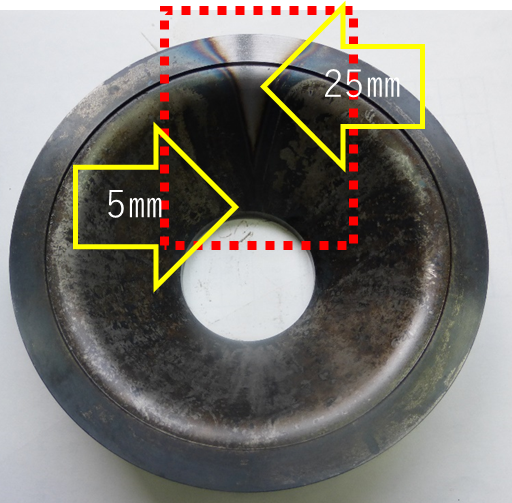
Fig.7のワークは、高周波焼入れで発生してしまう、ソフトゾーンの対策をレーザ焼入れを組み合わせることで、製品寿命を大きく伸ばした事例について紹介します。
Fig.7 のワークは、高周波の回転焼入れにて、内径テーパー部を焼入れ硬化させた写真になりますが、加工後、この赤枠部にソフトゾーンが発生しています。高周波焼入れでは、始点と終点部を重ねる事で、割れが出てしまう可能性があるため、始点と終点は重ならないように焼入れする必要性があります。また、この製品では、焼入れ部がテーパー形状のため、内径が小さい部分のソフトゾーン距離は約5mm、内径の大きい部分のソフトゾーン距離は、約25mmになります。このソフトゾーンというのは、読んで字のごとく「ソフト」=「軟らかい」、「ゾーン」=「範囲」ということで、本来なら、硬くなってほしい部分ですが、焼入れ硬化しない軟らかい範囲が残ってしまうことを言います。
この本来なら硬くしたい部分に、ソフトゾーンが残るとどうなるのかというと、その部分が部品の使用中に他の硬化された部分と比較して、非常に摩耗しやすいということになるため、製品寿命が短くなるということにつながります。
そこで、レーザ焼入れを組み合わせることで、どのように上記の課題を解決したのかを説明します。Fig.9は、高周波焼入れで発生したソフトゾーンを、レーザ焼入れで対策をしたあとの写真になります。ソフトゾーンであった部分に、レーザ焼入れを加工し、それを埋める形で、範囲を最小限にしました。その結果、ソフトゾーンの部分の異常摩耗が無くなり、製品寿命を延ばす事ができました。また、弊社では、高周波焼入れとレーザ焼入れを組み合わせる、この技術に対して、特許を取得しており、多くのお客様より好評をいただいております。
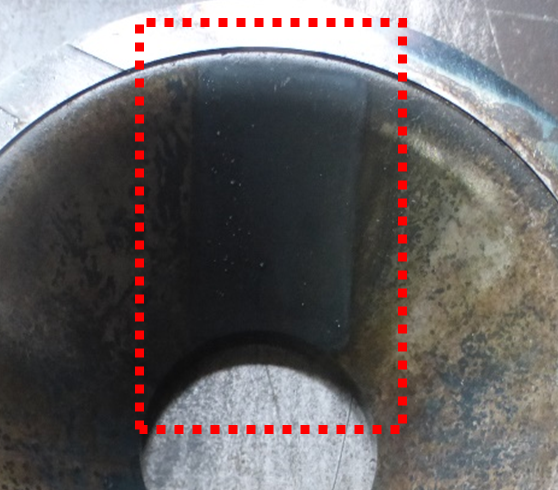
※特許第5945106 表面焼入れ層を有する鋼材部品及び鋼材部品に表面焼入れを行う方法
関連動画
3.まとめ
これまで、実際にあった課題解決の実例を基に、弊社での取り組みの説明を行いました。これらの課題解決により、高周波焼入れとレーザ焼入れの良いところを組み合わせながら、製品品質の上昇、製品寿命の上昇、コスト削減などを実現してきました。
レーザ焼入れでは、金属の部分焼入れで求められるすべての課題を解決できるわけではありません。しかし、適材適所のように、部分焼入れでも長所と短所を組み合わせていただくことで、これまで技術的に検討できなかった製品加工や、新しい発想での設計、課題解決の一助になれば幸いと考えております。
関連サービス
この記事の執筆者
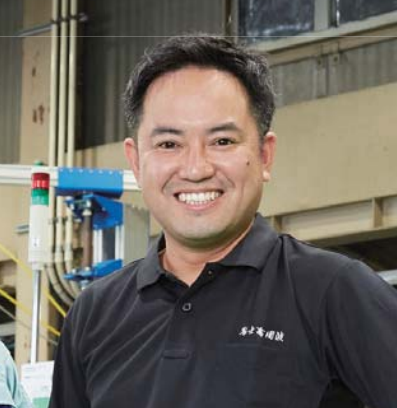
富士高周波工業株式会社 代表取締役
後藤 光宏
特級金属熱処理技能士/レーザ加工管理技術者名誉1級/滋賀県立大学 博士課程 在学中
小学生から大学までは野球漬けの日々を送る。
大学卒業後はポンプメーカーに1年間従事した後、2004年に富士高周波工業(株)に入社。
2008年からレーザ焼入れの開発に従事し、2018年に代表取締役に就任。
オンライン名刺はこちら