1.はじめに
今回は、レーザ焼入れにおいて、弊社が保有している設備について、半導体レーザ発振機・光学系・温度フィードバックシステムについての紹介をします。
2.高出力半導体レーザ発振機
2005年頃までは、焼入れに利用できるkw級の高出力を実現できるレーザはCO2レーザ(λ=10600nm)しかありませんでした。当時の炭酸ガスレーザは装置コストが高く、Fig.1で示されているように、鉄鋼材料へのレーザ光吸収率が、10%程度と低く、例えば、1000Wのレーザ光を照射したとしても、100Wしか光を吸収せず、900W分のレーザ光は反射してしまいます。そのため、CO2レーザで、レーザ焼入れを行うためには、かなりの大出力のレーザ発振器を準備するか、鉄鋼材料の光の吸収率を上げるために、グラファイトなどの吸収剤(黒体塗料)を照射部に塗布をする必要性がありました。そのため、吸収剤の塗布工程がコストの増大につながりました。これらの理由により技術的には、確立されていたのにも関わらず、レーザ焼入れ市場が広まらなかったものと考えます。
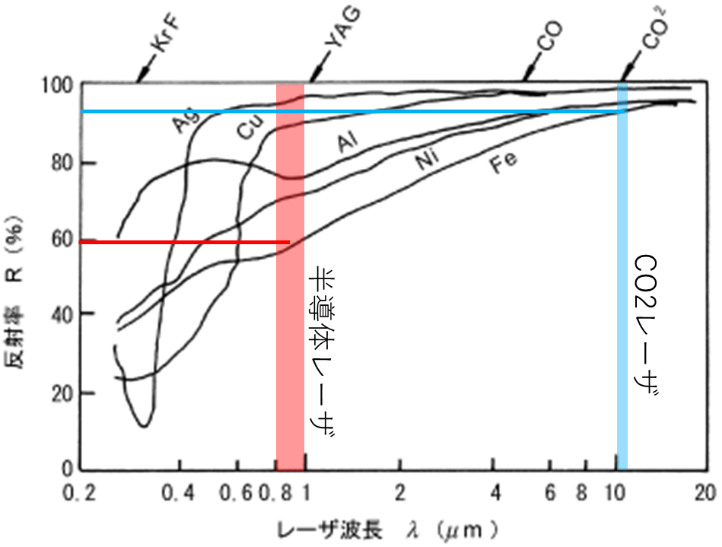
(社)日本溶接協会 2004
しかし、2000年頃から高出力の半導体レーザ(λ=800~1100nm)が市場に登場してきました。鉄鋼材料への吸収率は60%程度とCO2レーザと比較しても、5倍以上レーザ光の吸収率に優れています。同じ出力を投入したとしても、1/5の出力で、金属を同等まで加熱することができます。よって、一般的には、吸収剤の塗布も必要としません。消費電力の面で比較しても、高出力半導体でのレーザ焼入れは優れています。熱処理の業界では、高周波焼入れは、省エネな熱処理と言われていますが、50KW、100KWクラスの発振機が一般的な出力帯となり、多くの電力量を必要とします。しかしながら、高出力半導体レーザは消費電力量も非常に少なくなります。例えば、1KW出力のファイバー伝送タイプの半導体レーザでフルパワー照射したとしても消費電力は3.5kw程度で、他の熱処理工法と比べて、極めて省エネな熱処理方法になります。
弊社は、7台の半導体レーザ発振機を保有しています(Table1)。
【Table1 富士高周波の半導体レーザ設備】※2021年7月現在
機種名 | 最大出力 | 特徴 |
LDF5000-100 | 5KW | 温度FBシステム使用可能 LDM4000との同時照射可能 |
LDF4000-40 | 4KW | 4mの製品の移動焼入れ可能 LDM1000との同時照射可能 |
LDM4000-100 | 4KW | 出張焼入れ可能 |
LDM3000-100 | 3KW | 量産品に対応 |
LDM1000-40 | 1KW | LDF4000との同時照射可能 |
LDF12000-100/4800-8 | LDモード12KW ハイブリッドモード LD 4KW Co 4.8KW |
半導体レーザとコンバータレーザの同軸照射可能 アルミの低スパッタレーザ溶接 |
ALPION | 300W | 直噴型マルチレーザクラッド 最小ビート幅 0.4mm 最小高さ 0.05mm |
レーザ発振機6台はドイツのLaserLine社製の発振機を使用し、1台は国内製です。低出力から、高出力まで、様々なラインナップを取り揃えており、製品に最適なレーザ発振機の選択が可能です。LaserLine社製発振機の種類は大きく分けて2種類あります。Fig.2のLDFタイプ大型冷蔵庫位のサイズ感です。
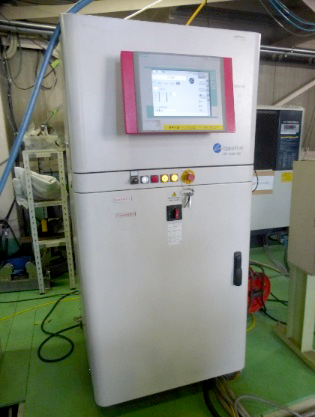
Fig.3は、LDMタイプになります。特にLDM タイプは非常にコンパクトな発振機となっており、19インチラックに収まるサイズ感で、レーザ焼入れシステムを製作した場合、システムの中に組み込むことが可能です。
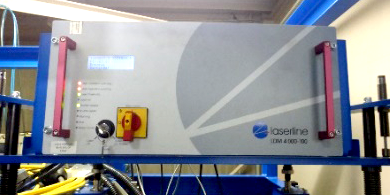
また、Fig.4のハイブリッドレーザは半導体レーザとコンバータレーザの同軸照射が可能です。同軸照射をすることで、レーザ溶接時のスパッタを低減することができます。実績として、欧州でアルミの低スパッタレーザ溶接用途で活用されています。
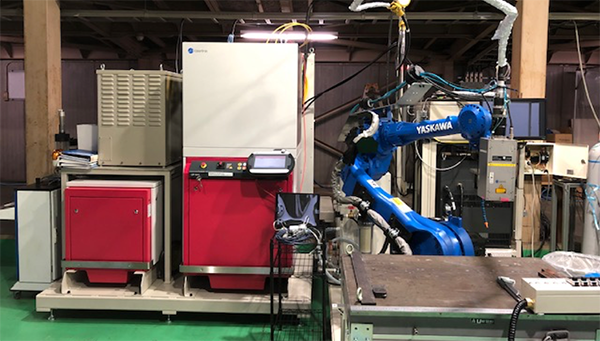
最後にFig.5は村谷機械製作所製の直噴型マルチビームレーザクラッディングシステムのALPIONです。精密部品への低入熱なレーザクラッティング施工が可能で、最小ビート幅が0.4mm、最小クラッティング高さが0.05mmになります。
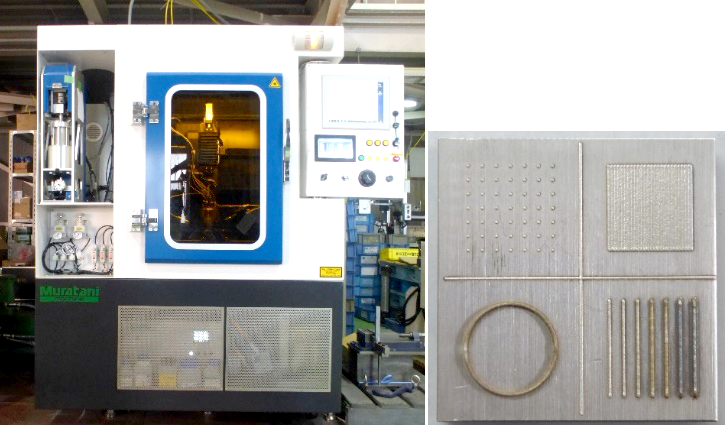
※右写真 肉盛りサンプルワーク(50×50×10t)
国内ではLaserLine社製の発振機取り扱い実績が多い商社として、丸文(株)があり、メンテナンス等は、グループ会社である㈱フォーサイトテクノが請け負っています。メンテナンスに関しては、1~2年に1回フィルターの交換や出力チェック等、半日~1日程度で完了します。
バーチャル工場見学動画
3.レーザ焼入れにおける光学系
レーザ焼入れにおいて、光学系の選定は重要です。光学系の種類によって、スポットサイズが変化し、焼入れ結果(焼入れ幅や硬化深さ)が変化します。高周波焼入れで言えば、焼入れをする際にどのような形状のコイルを選択するかと同じ意味合いをもっています。よって、レーザ焼入れにおいて、どのようなスポットサイズを用いて焼入れをするかというのは、重要な要素になります。また、色々な製品の焼入れに対応するためには、様々なスポットサイズを作れるメーカーが良いと考えます。その点では、LaserLine社は、様々なスポットサイズのラインナップを取り揃えており、多品種少量及び、試作開発等で活躍します。LaserLine社では、スポットサイズが固定される標準型(Fig.6)とスポットサイズが自在に変更できるズームホモジナイザー(Fig.7)と言われる2種類の光学系があります。量産等でスポットサイズを変化させる必要性が無い場合は、標準型の光学系を推奨します。また、汎用的に多品種小ロットでレーザ焼入れを実施する場合は、ズームホモジナイザーを推奨します。
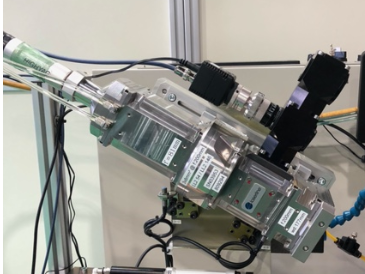
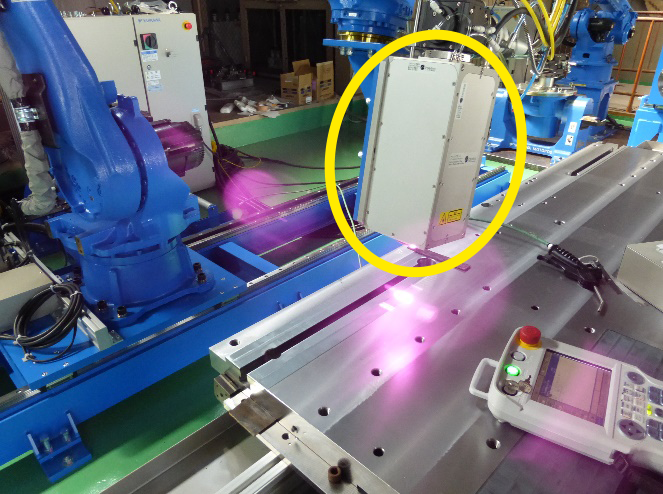
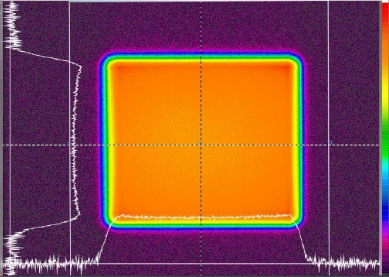
下段 ビームプロファイルデータ(18㎜×14㎜)
弊社においては、標準光学系で約100種類のビーム形状を作ることが可能です。ズームホモジナイザーは、4台保有しています。1軸タイプのMAXの光軸はX軸6.5mm Y軸116mm、2軸タイプのMAXはX軸38mm Y軸38mmまでは、対応可能となっており、様々なユーザーの要望にこたえることが可能な光学系ラインナップとなっています。
関連動画
4.レーザ焼入れの温度フィードバック制御
熱処理において、「熱処理温度の管理」は品質保証をする上で、非常に重要な項目となっています。それは、レーザ焼入れにおいても同じ事が言えます。ただし、高温域の温度帯を正確に測定することは非常に難しく、レーザ焼入れにおいては、参考値程度で考えることが一般的です。ただし、ワークの表面状態や、外乱などの要因が一定であれば、再現性は高いと言えます。しかし、ワークにはそれぞれバラつきがあり、また、煙などの影響を受けやすいため、焼入れ温度の真値というのは、わかりません。ただし、それらのばらつきをすべて考慮した設定温度にすれば、十分使えることができるレベルの機器は弊社も保有しており、様々な試作で利用しています。レーザ焼入れにおいて、一般的に使われる温度計は、放射温度計です。光学系内に組み込み、光学系を通して直接温度を読み取り、レーザ発振機にその温度をフィードバックし、温度が常に一定になるように、出力をコントロールします。Fig.8にあるテストピースにおいては、ズームホモジナイザーにて焼入れ中にスポットサイズを変化させています。
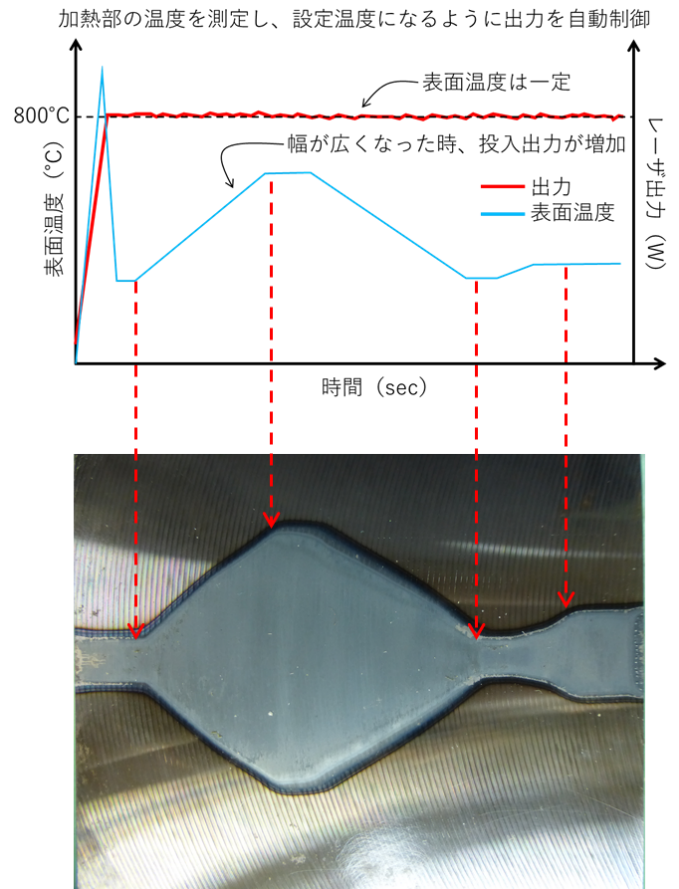
そのため、大きいビームから、小さいビームに変化する中で、出力が同じであれば単位面積当たりの出力値が上がり、温度が上昇します。そのため、同じ温度になるように「出力値を下げなさい」という命令をレーザ発振機に出力し、レーザの出力が下がります。この一連の動作を10msに1回のサンプリング数で行い、温度を安定化させるのが温度フィードバック機器になります。この温度フィードバック機器が活躍する場面としては、スポットサイズは途中で変わらないが、ワークの肉厚が途中で変わるため、同じ出力値であっても温度が上がったり下がったりするようなケースがあれば、非常に有効です。また、スポットサイズが途中で変わるような際にも同じく有効です。量産などでは、フィードバックはせずに温度だけを測定し、品質管理の一つのセンサーとしての利用価値も大いにあります。
5.まとめ
ここまで、富士高周波におけるレーザ焼入れの設備について、述べてきました。本来であれば、ロボットシステムについてや焼入れシステムについても解説したかったのですが、設備ノウハウも含んでいるためここでは、説明はひかえさせていただきます。さらに深い設備情報を得たいと言うことであれば、ぜひとも弊社まで会社見学に来て頂き、直接レーザ焼入れの現場を見て頂けたら、さらに理解も深まるかと思います。
関連サービス
この記事の執筆者
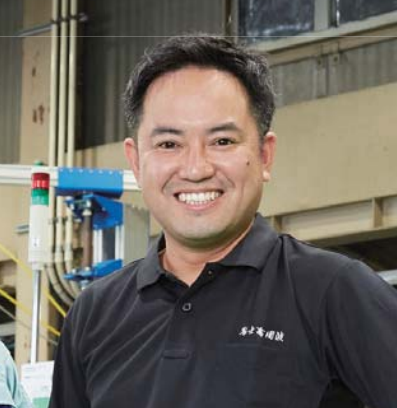
富士高周波工業株式会社 代表取締役
後藤 光宏
特級金属熱処理技能士/レーザ加工管理技術者名誉1級/滋賀県立大学 博士課程 在学中
小学生から大学までは野球漬けの日々を送る。
大学卒業後はポンプメーカーに1年間従事した後、2004年に富士高周波工業(株)に入社。
2008年からレーザ焼入れの開発に従事し、2018年に代表取締役に就任。
オンライン名刺はこちら