1.はじめに
今回は、レーザクラッディングの設備について、粉末供給機、クラッドノズル、フィードバックシステム(E-Maqs)について解説します。レーザ発振器に関しては、技術レポート「レーザ焼入れ設備」の資料を参照して頂ければと思います。
以下、レーザクラッディングを“LC(Laser Cladding)”と表記します。
2.LCシステム
2-1 LCシステム全体像
システムの全体像に関しては、「レーザクラッディングの基礎」2-3項を参照下さい。
2-2 粉末供給機(パウダーフィーダー)
LC施工を行う上で、パウダーを供給し施工をする必要があるため粉末供給機(Fig.1)は必須になります。
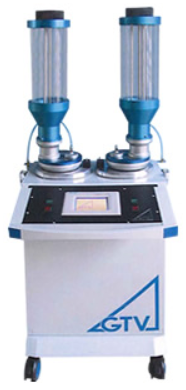
弊社保有のGTV社製パウダーフィーダーはパウダーの正確な送給量と再現性が得る事ができます。1塔式(パウダーホッパー1本)から最大4塔式まで増設が可能となります。ホッパーを増設することで、肉盛り材料を任意の割合で混ぜながら供給することが可能です。例えば、ステライト粉末にタングステンカーバイト(WC)を10%程度混ぜて供給することで通常のステライトよりも高い耐摩耗性を得ることができます。以上のように様々な粉末を混ぜる事で、肉盛り材の様々な特性を出すことが可能となります。また、ホッパーには粉末がホッパー内部で凝集しない様に撹拌用のミキサーが標準装備されています。粉末をノズルに供給するためにキャリアガス(アルゴンもしくは窒素)を利用します。キャリアガスの流量は、マスフローコントロール制御されており、粉末を安定的にノズルまで供給できるようになっています。最後に正確に定量の粉末を供給するための回転式ディスクがあります。ディスクには、一定のサイズの溝があり、その溝に粉末が充填され、キャリアガスと共にノズルまで供給されます。粉末量を制御しているのは、ディスクの回転量(rpm)と溝の深さや幅になります。ディスクの回転数を上げれば、供給粉末量が増加します。ディスクの溝のサイズにも様々なサイズがあり、溝のサイズでのパウダー量の制御も可能となります。弊社における一般的なLC施工の際には、20g/min程度のパウダー供給量になります。
2-3 クラッドノズル
パウダーフィーダーから運ばれたパウダーをレーザ光と同軸に供給させます。ノズルには様々な種類が存在し、パウダー・冷却水・シールドガスを供給するポートがあります。レーザクラッティングにおいてノズルの選択が重要になり、下記記載の3種類は弊社保有のクラッドノズルになります。
まずは、Fraunhofer IWS製のCOAX8(Fig.2)になります。

COAX8の特徴として、Fig.3のように360°全周に切られているスリットから粉末が供給されます。Fig.4は、粉末を供給しているところを横から見た図になります。粉末は、ノズルの先端から約15mmの位置で焦点を結ぶように設計されており、粉末の焦点と加工の焦点は一致します。COAX8は、基本的に2Dでの肉盛りに対応しており、ノズルの傾きも最大±30°まで対応となっています。弊社で保有しているビーム形状との組み合わせは、矩形で10種類、丸型で20種類となり、ビーム形状の選択肢が最も多くなります。


次にCOAX8のデメリットです。まず一つ目として挙げられるのが、ノズルの先端と加工点までの距離(以下WDと記載する)は、15mmと短く肉盛り時のスパッタなどの影響でノズル先端のスリット部に溶融粉末が詰まる可能性があります。しかし、ノズル先端の消耗品の価格は他のノズルと比較しても安価となっております。2つめのデメリットとしては、弊社保有のCOAX8は型番が古いため、Fig.4のようにノズル先端の径が太く(φ79)なっています。そのため、奥まった部分への肉盛りとなると、ヘッドが干渉してしまい形状によっては、肉盛りができない場合があります。
Fig.5は、5mm×5mmのビーム形状使用時の肉盛り外観となります。外観は、小高い丘のようになっています。表面は少しざらついた状態になっています。Fig.6は、切断マクロ写真となります。肉盛り高さは中央部で焼き1mm、肉盛り幅は約5mmとなっています。矩形のビームを使っているため、希釈は均一になっています。


次に紹介するのは、Fraunhofer IWS製のCOAX11(Fig.7)です。COAX11の特徴として、幅の広い肉盛り(19mm)が可能となり、他の肉盛りノズルと比べても圧倒的な肉盛速度(675cm3/h)が実現できます。

粉末の供給は、Fig.8のように前後に大きく切られたスリットがあり、そこから粉末が供給されます。Fig.9のように前後方向からライン状のパウダーを供給する構造で、かつWDが30mmと広くなるので、スパッタの影響でノズルの先端が詰まりにくい構造となっております。また、使用時は高出力レーザが必要(Min5KW以上)で、0.3mm以下の肉盛りは不得意となります。また、COAX11もCOAX8と同じく2D仕様となっています。
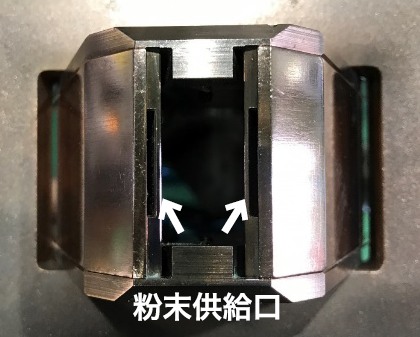

Fig.10は19mm×5mmのレンズ使用時の肉盛り外観となっており、弊社が保有するノズルでは、最大17mm幅の肉盛りが可能です。Fig.11は切断マクロ写真となります。肉盛り高さは、約1mmとなっています。希釈も幅全域にわたって均等に希釈しています。
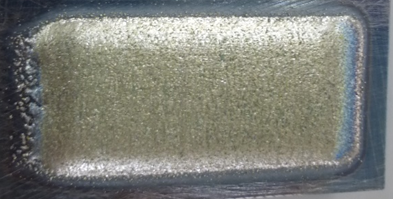

関連動画
最後にGTV社製のPN6625(Fig.12)になります。

COAX8、11との大きな違いとして、90°傾けての肉盛り施工が可能という点になります。なぜ、90°傾けての加工が可能なのかというと、粉末の供給がFig.13のように円周上に空けられた6つの小さい穴化から粉末が出てくるため、弊社データでは、COAX8と比較した場合、Fig.14のように粉末の飛翔速度が約4倍となっています。ノズルを傾けたとしても粉末は重力に負けず加工点まで供給されます。しかし、そのデメリットとして粉末の飛翔速度が早ければ、空中で粉末が溶けにくくなるので90°に傾けた時の歩留まりは悪くなる傾向にあります。また、PN6625はハイスピードレーザクラッディングにも対応できるノズルとなります。しかし、ビームの選択肢がCOAX8 と比較して少ないなどのデメリットもあります。

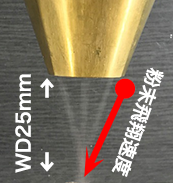
Fig.15がφ5のビームを使用しての肉盛り外観となります。外観は、COAX8で5mm×5mmの肉盛りしたものとあまり外観による差は有りませんが、Fig.16 のように丸ビームを使用しているため、中央部の希釈が大きくなりやすいという傾向があります。
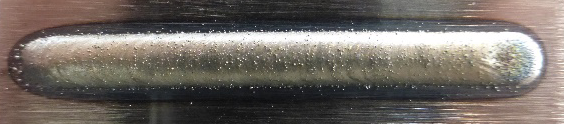
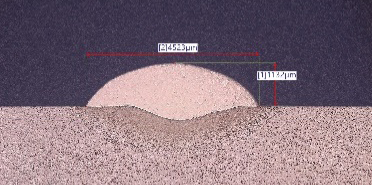
関連動画
2-4 カメラベース温度フィードバックシステム
LC施工を連続的に行えば、基材にどんどん熱がたまってきます。基材に熱がたまってくると、基材の溶け込み量が増加してしまい、最初と最後では、基材の希釈量が変わってきてしまいます。施工の初めは、希釈率が10%前後にコントロールされていたのに、施工の最後の方では、同じ条件で施工しても基材に熱がたまってしまうため、希釈率が20%を超えるという状態になります。希釈率が変わるという事は、肉盛材の特性が変わるという事なので、品質トラブルになる可能性があります。そのため、連続的な施工の時には、レーザの出力を制御する必要性があります。
弊社が保有しているFraunhofer IWS社製のE-MaqS(Fig.17)は、LC施工における溶融池サイズを測定し、レーザへフィードバックすることにより出力制御を行い、プロセスの安定化を図るフィードバック制御装置です。フィードバックしない時(Fig.18)とした時(Fig.19)では希釈率に差が出ます。

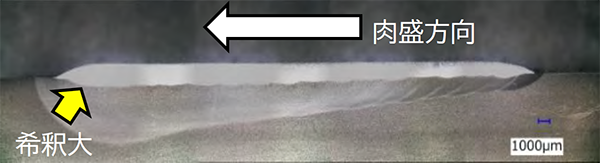

【参考資料】
富士高周波保有のレーザクラッディング用ノズル一覧はこちら
バーチャル工場見学動画
関連サービス
この記事の執筆者
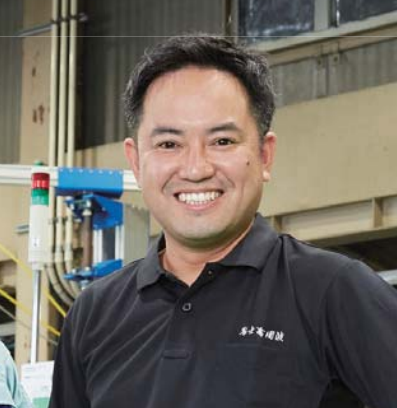
富士高周波工業株式会社 代表取締役
後藤 光宏
特級金属熱処理技能士/レーザ加工管理技術者名誉1級/滋賀県立大学 博士課程 在学中
小学生から大学までは野球漬けの日々を送る。
大学卒業後はポンプメーカーに1年間従事した後、2004年に富士高周波工業(株)に入社。
2008年からレーザ焼入れの開発に従事し、2018年に代表取締役に就任。
オンライン名刺はこちら